Take a nice look around you, and you'll find yourself surrounded by commonplace metal objects for everyday use. From the rims of your bicycle to your microwave and kitchen equipment, metal has been a critical component for domestic, commercial, and industrial usage.
The word metals include many kinds of metal. From the more common ones like zinc, copper, and aluminum to rare metals like gold, silver, and palladium, the metal family exists in abundance in the earth's crust, which is mined and extracted to be used to make products that simplify our everyday lives.
But every metal has its own shortcomings. For one, almost all kinds of metals are prone to corrosion and rusting. This is where metal finishing comes in.
What is Metal Finishing?
Metal finishing refers to the process of altering the surface of metals to achieve resistance and polish. There are multiple methods for metal finishing, though all of them are employed once a part consisting of metal is manufactured. Electroplating, powder coating, and abrasive blasting are some common metal finishing methods used for surface treatment.
There are various kinds of metal finishing, and you must choose the right kind of metal finish depending on the type of metal surface. The kind of metal finishing used would depend on the end usage of the product.
Metal finishing adds durability to a product and also beautifies them. But the benefits don't stop here. Let's take a look at why metal or surface finishing is needed.
Importance of Metal Finishing
Metal finishing isn't simply intended to add aesthetic value to a product. They're primarily used to provide a protective layer over the surface. Significant benefits of metal finishing include:
-
Enhances Attractiveness
Every commercial product has to have a certain degree of aesthetic appeal added to it. In some industries, how a product looks may be equally important as its function. Metal finishing adds aesthetic value to metal products.
-
Increases Corrosion Resistance
Harsh weather elements pose a considerable risk to metal products. One of the biggest problems is corrosion, which decreases not only the appearance of the product but also its performance. Surface finishing ensures surface protection against corrosion and increases its life.
-
Protects Against Chemicals and Wear
Apart from corrosion resistance, metal finishing also protects the product from harsh chemicals and the effects of wear.
-
Improves Overall Performance
Metal finishing also improves the strength and performance of the product. Surface finishing is also used in industries to improve the conductivity of metals.
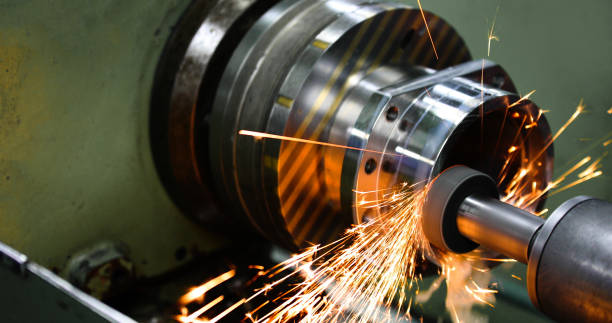
Kinds of Metal Finishing
There are various kinds of metal finishing processes, each having a distinct effect on the surface. These are the different types of metal finishing used across industries today:
-
Electroplating
Electroplating involves using a direct electric current to reduce cations on a surface and deposit metal coating on the substrate.
-
Electroless Plating
Also known as chemical plating, electroless plating is the deposition of metal coating on solid substrates using an autocatalytic chemical reduction of cations in a liquid bath.
-
Electrocoating
Electrocoating or e-coating refers to the process where wet paint adheres to a metal surface via an electrical current.
-
Passivation
Passivation is the chemical treatment of alloys to enhance their corrosion resistance and clean off the surface to get rid of contaminants.
-
Case Hardening
Case hardening is a process of hardening the upper layer of metal while allowing the layers underneath to remain soft. Also called surface hardening creates a sturdy layer of metal on top and is primarily used in automotive and mechanical engineering processes.
-
Powder Coating
A finishing process that causes the dry powder to adhere to a surface via an electric charge. The component is then baked in an oven for a uniform coating.
-
Electropolishing
Electropolishing is an electrochemical process that removes the outermost skin of a metal surface. This process is used to rectify imperfections on the surface.
-
Buff Polishing
Buff is a tool made of cotton that polishes a surface to finish it. Buff polishing is mainly done on stainless steel components.
-
Metal Grinding
Metal grinding is an abrasive process used to finish metal components and provide a smooth finish with sharp edges. Predominantly a metal-cutting process, metal grinding is used in mineral and cement industries.
-
Abrasive Blasting
Abrasive blasting involves propelling abrasive materials like sand onto a surface at high pressure to smoothen or reshape a surface and also to remove contaminants.
Industrial Applications of Metal Finishing
Surface finishing is widely used across various industries today. They've become a key component of the manufacturing process across industries like:
- Automotive
- Hardware
- Home Appliances
- Heavy Industrial Machinery
- Electronics
- Aerospace
- Telecommunications
- Jewelry
Benefits of Metal Finishing
Metal finishing increases the life and durability of products. Without this treatment, we would see a sharp decline in the lifespan of metals due to corrosion and other elements. Finishing is also used to shape or reshape components, improve adhesiveness with coatings, and alter the conductivity of the metal product. Non-metal components made of wood or glass, like furniture, are also subjected to finishing for beautification.
All-in-all, surface finishing confers the following benefits to metal products:
- Corrosion Resistance
- Wear Resistance
- Chemical Resistance
- Improved Electrical Conductivity
- Improved Appearance
- Hardness
- Solderability
Powder Coating is the Most Widely Used Industrial Metal Finishing Process
Industrial coating mainly includes a liquid that's sprayed or painted over a surface. The one exception here is powder coating. This powder-based alternative is all the rage and is used by small job shops to large metal finishing establishments owing to their numerous benefits.
Powder coating provides greater surface thickness while adding a distinct aesthetic beauty. This form of the coating doesn't require additional layers over the surface, making them more suitable and cost-effective for batch products.
Powder coating is sprayed electrostatically over the surface using a spray gun. The coated component is then cured in a high-temperature oven, which causes the powder to bind to the surface without dripping.
Rusty Lions: Your One-Stop Shop for Metal Finishing in New Jersey
Rusty Lions is the most reliable metal finishing and powder coating provider in New Jersey. We're among the few companies offering metal finishing and refinishing services throughout New Jersey with bespoke services to meet the varying needs of industries, machinists, job shops, etc.
Contact us to learn more about our metal finishing and powder coating services.